The Reusable Messenger Bag
For the final design, a so-called reusable 'messenger bag' was developed as it's a durable, relatively cheap and functional product that's already trusted among KPN mechanics. The exterior and casing of the messenger bag is made of 100% polypropylene, which is water- and dust-proof, while allowing for excellent recyclability. The interior is a soft padding, made of recycled felt, to ensure protection throughout the delivery process. The cables and accessories that come with the device are separately stored in a pouch, to improve overview and workflow during installation. The bag is opened with a roll-top, which is secured by velcro and two buckles. This option is cheaper and more durable then a zipper. The packaging has three designated sticker areas for the 6-8 stickers it needs during one use cycle. This sticker area is made of a special under-layer (Swaplabel) that allows for easy label removal after use.
For the final design, a so-called reusable 'messenger bag' was developed as it's a durable, relatively cheap and functional product that's already trusted among KPN mechanics. The exterior and casing of the messenger bag is made of 100% polypropylene, which is water- and dust-proof, while allowing for excellent recyclability. The interior is a soft padding, made of recycled felt, to ensure protection throughout the delivery process. The cables and accessories that come with the device are separately stored in a pouch, to improve overview and workflow during installation. The bag is opened with a roll-top, which is secured by velcro and two buckles. This option is cheaper and more durable then a zipper. The packaging has three designated sticker areas for the 6-8 stickers it needs during one use cycle. This sticker area is made of a special under-layer (Swaplabel) that allows for easy label removal after use.
Decreasing product damage
During the research, it was found that electronics are potentially damaged due to improper use of return packaging during the rough logistic journey. By consistently providing the right return packaging to the mechanic, electronics could be packaged more safely and therefore decrease the product damage. By introducing a reusable packaging, in combination with an efficient supply system, the product damage could potentially be reduced with an estimated 5%. This not only enables a better circularity of electronics, but also saves significant costs.
During the research, it was found that electronics are potentially damaged due to improper use of return packaging during the rough logistic journey. By consistently providing the right return packaging to the mechanic, electronics could be packaged more safely and therefore decrease the product damage. By introducing a reusable packaging, in combination with an efficient supply system, the product damage could potentially be reduced with an estimated 5%. This not only enables a better circularity of electronics, but also saves significant costs.
Reducing packaging waste and environmental footprint
The reusable messenger bag is made to replace the current single-use packaging that’s used to package refurbished devices of KPN. It is estimated that the reusable saves around 0.8 kg of cardboard and plastic waste per trip. In its entire lifetime, the reusable packaging has the potential to reduce 8kg’s of CO2. This results in an environmental CO2 break-even between 4 - 7 use cycles.
The reusable messenger bag is made to replace the current single-use packaging that’s used to package refurbished devices of KPN. It is estimated that the reusable saves around 0.8 kg of cardboard and plastic waste per trip. In its entire lifetime, the reusable packaging has the potential to reduce 8kg’s of CO2. This results in an environmental CO2 break-even between 4 - 7 use cycles.
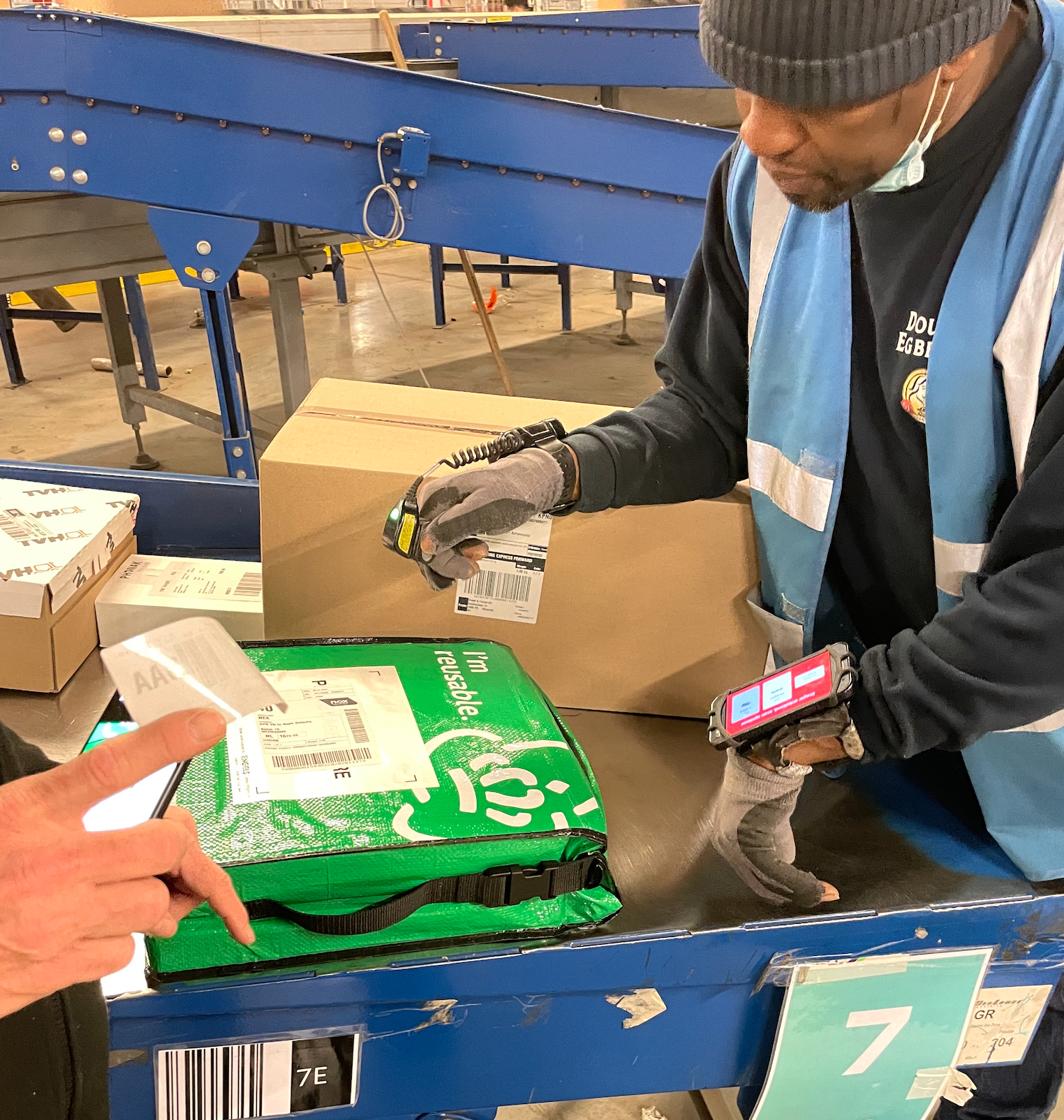
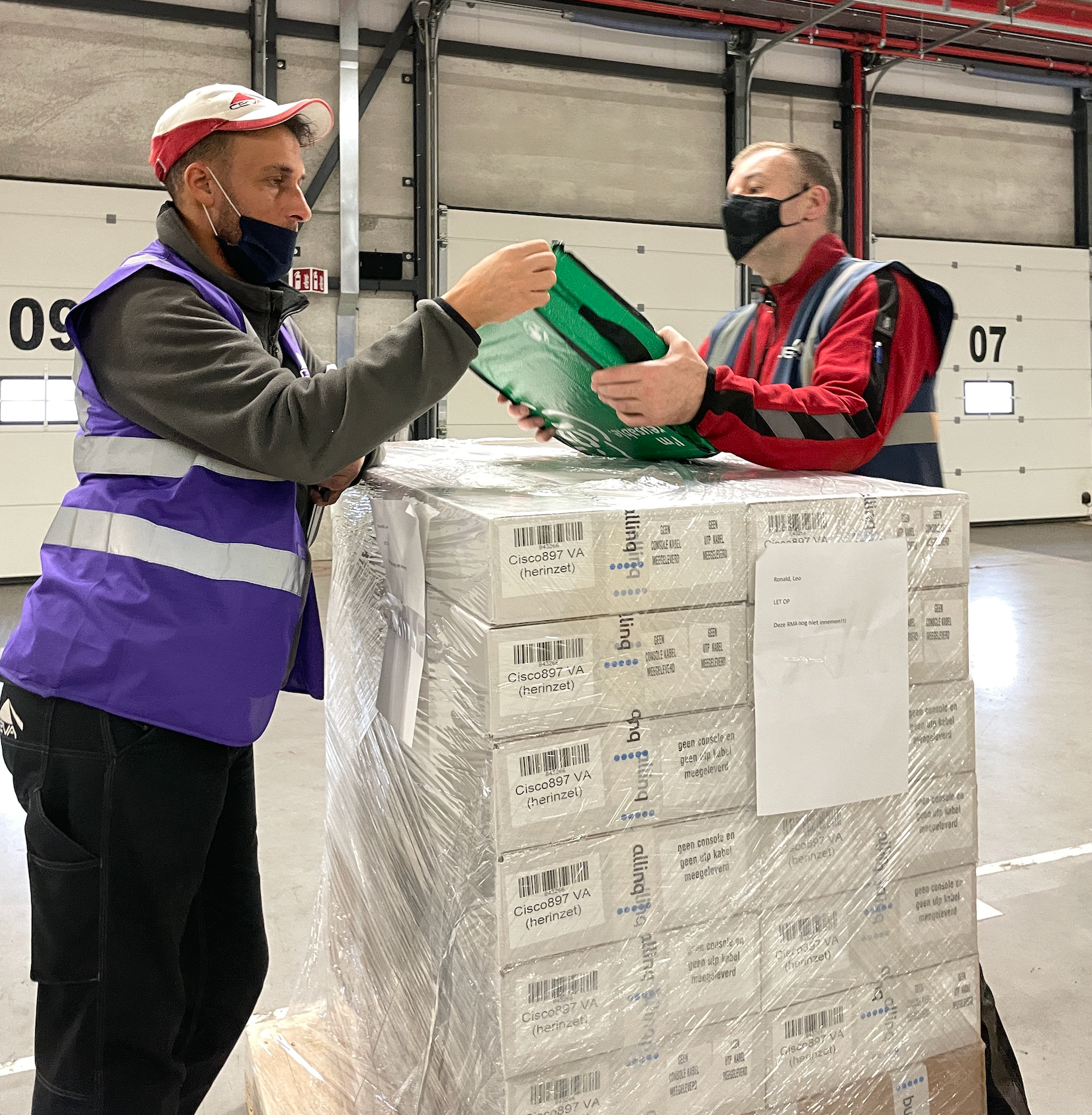
A first, successful implementation using only existing logistic processes.
The accessibility of logistics, workflow of employees and the functionality of the product were tested in an actual orders of KPN's B2B market. In this first technical implementation, a networking device including reusable packaging was sent to the client and installed, after which the empty reusable package was sent back. Along the way, all involved distribution stages were observed and employees were interviewed. This small-scale pilot showed a successful forward and return trip of reusable packaging using only existing processes, validating the KPN’s logistic resilience to such a concept.
The accessibility of logistics, workflow of employees and the functionality of the product were tested in an actual orders of KPN's B2B market. In this first technical implementation, a networking device including reusable packaging was sent to the client and installed, after which the empty reusable package was sent back. Along the way, all involved distribution stages were observed and employees were interviewed. This small-scale pilot showed a successful forward and return trip of reusable packaging using only existing processes, validating the KPN’s logistic resilience to such a concept.
Supply Chain Design for Reusability
For a successful implementation of reusable packaging, I developed a solid supply and distribution model that ensures the right packaging, at the right location and time. This 'system architecture' is build with only existing forward and return processes of KPN and also tested in the pilot.
For a successful implementation of reusable packaging, I developed a solid supply and distribution model that ensures the right packaging, at the right location and time. This 'system architecture' is build with only existing forward and return processes of KPN and also tested in the pilot.
The distribution concept revolves around the mechanic, as he is the initiator of the return process (the mechanic-centred system architecture). In this system, the mechanic will act as the orchestrator of the packaging, as he receives, stores and returns the supply from his working vehicle. By ensuring a stockpile of empty packaging at mechanics' premises at all times, he can always return his electronics with proper packaging that communicates and encourages the desired return guidelines.
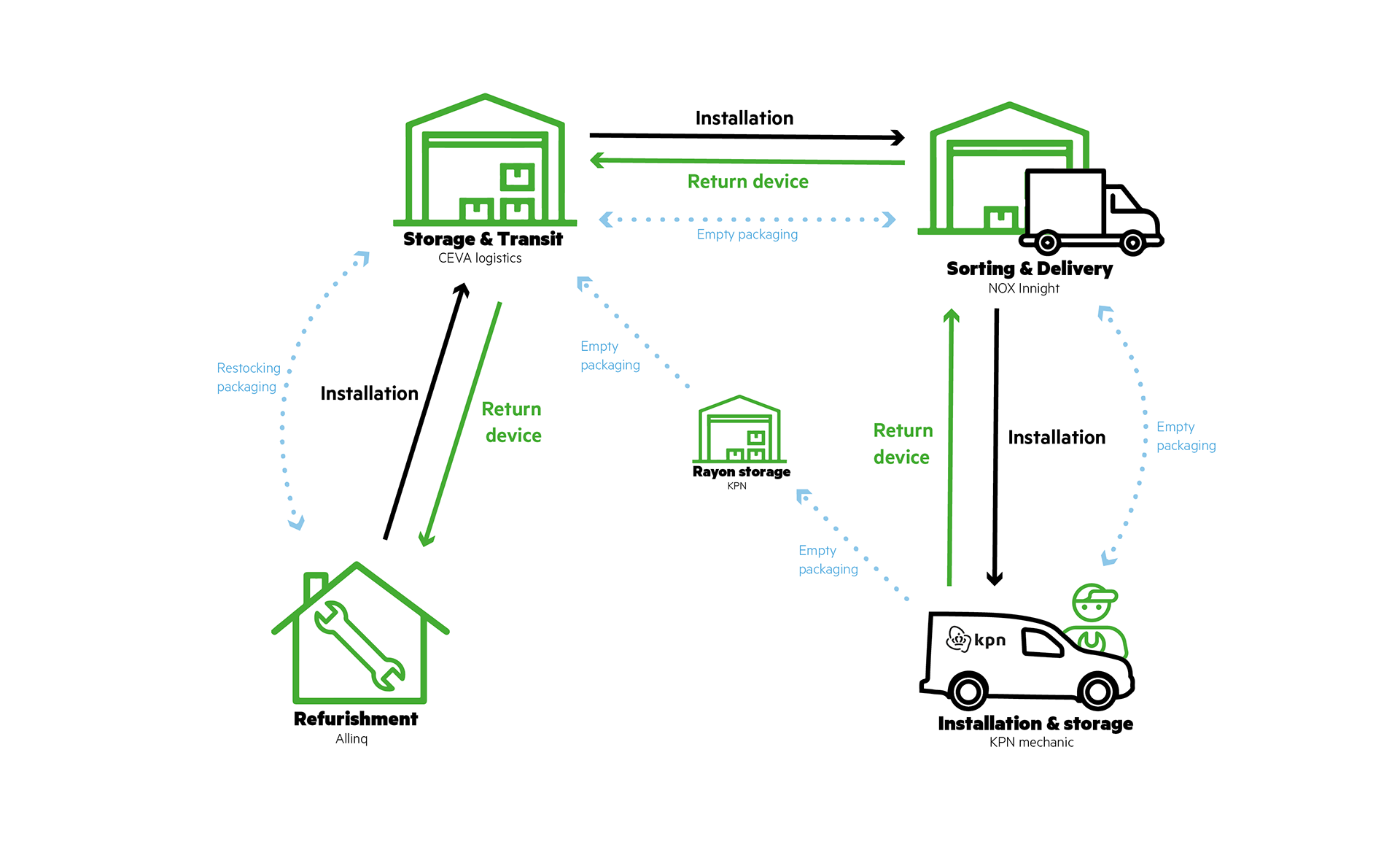
A prototype driven design process...
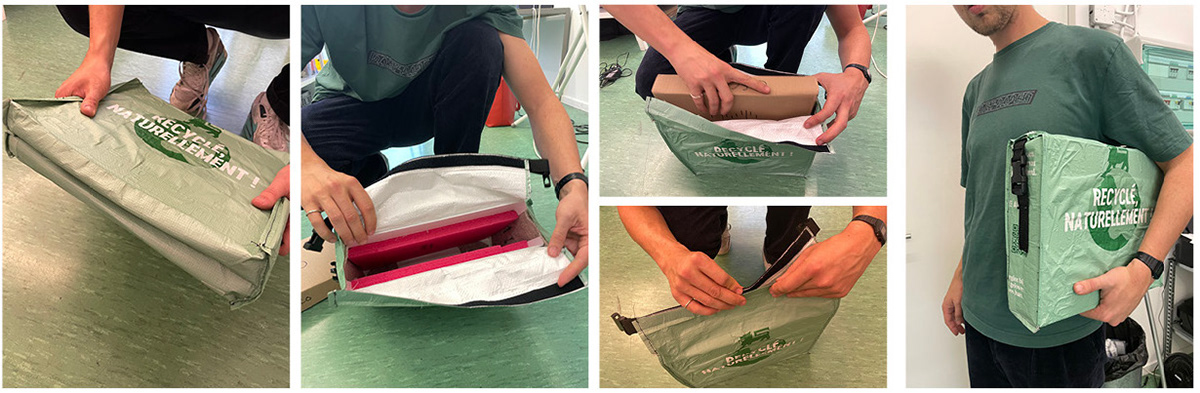
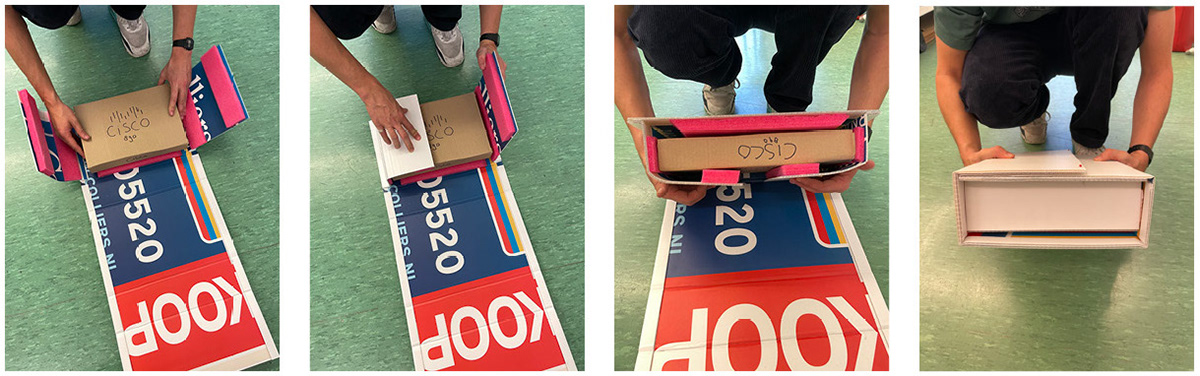
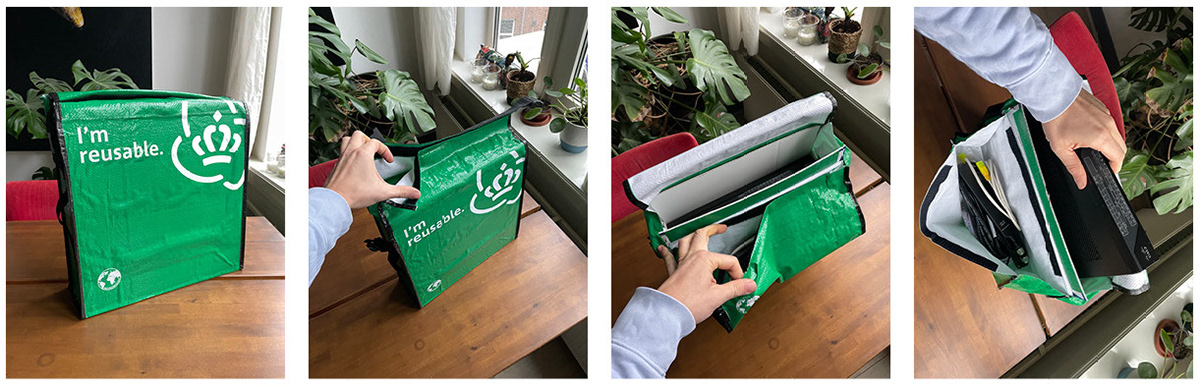